Zaawansowane usługi przemysłowe w WZL Nr 2 S.A. w Bydgoszczy
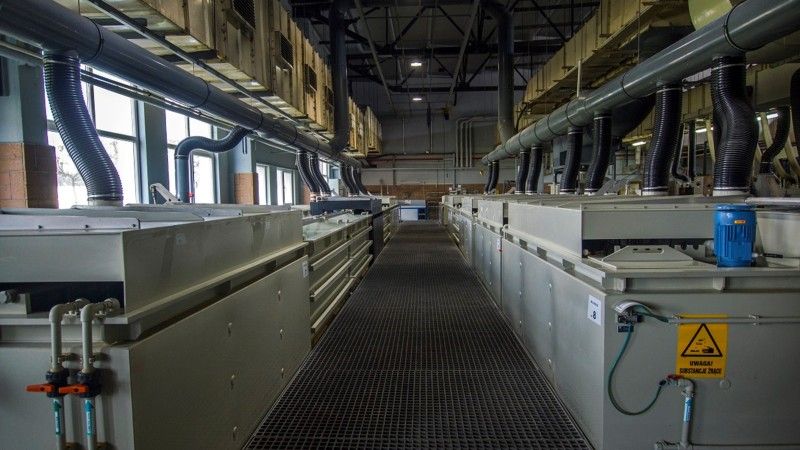
Wojskowe Zakłady Lotnicze Nr 2 S.A. od lat produkują części zamienne do różnego typu statków powietrznych służących w Siłach Zbrojnych RP. Jako producent części lotniczych posiadają ogromne kompetencje i możliwości prowadzenia precyzyjnych prac.
Artykuł sponsorowany. Partnerem materiału są Wojskowe Zakłady Lotnicze Nr 2 S.A.
W ciągu lat konsekwentnego rozwoju w zakładach w Bydgoszczy powstał jeden z najnowocześniejszych obiektów dostosowanych do tego typu prac, tworzony przez zespół wysoko wykwalifikowanych specjalistów dysponujących dostępem do zaawansowanych technologii, narzędzi oraz stale unowocześnianą infrastrukturą.
Obróbka galwaniczna
Usługi galwaniczne są niezbędne do ochrony podzespołów samolotów przed korozją, która może spowodować znaczne uszkodzenia i zagrozić bezpieczeństwu statku powietrznego, które często są narażone na trudne i ekstremalne warunki. Proces ten obejmuje nałożenie powłoki, która działa jako warstwa protektorowa, chroniąc metal przed korozją. Dodatkowo może być zabezpieczona powłoką organiczną, zwiększając tym samym odporność na działanie czynników zewnętrznych.
Wojskowe Zakłady Lotnicze Nr 2 S.A. świadczą wysokiej jakości usługi z zakresu obróbki galwanicznej zarówno na potrzeby własne, jak i dla przedsiębiorstw z różnych gałęzi przemysłu, np. kosmicznego, lotniczego, kolejowego, motoryzacyjnego, przetwórstwa tworzyw sztucznych, papierniczego. Stale modernizowana infrastruktura umożliwia nakładanie nie tylko standardowych, ale także unikatowych powłok galwanicznych. Zakłady WZL Nr 2 posiadają także certyfikaty uprawniające je do przeprowadzania takich prac jak anodowanie, czyli procesu utleniania powierzchni aluminium i jego stopów w kąpieli na bazie kwasu siarkowego. W efekcie powstała warstewka tlenków może stanowić dobrą ochronę przed korozją. Poprzez barwienie podnosimy wartość dekoracyjną powłoki. Oprócz tego istnieje możliwość wykonywania anodowania twardego, dzięki czemu powierzchnia aluminium zwiększa swoją odporność na ścieranie oraz podnosi twardość. W tym przypadku można nakładać grubsze warstwy nadające się do docierania na pożądany wymiar. Powłoki anodowe mają jeszcze jedną cechę – są izolatorami elektrycznymi.
Firma posiada również inne obróbki galwaniczne, takie jak: chromianowanie aluminium, cynkowanie, fosforanowanie cynkowe drobnokrystaliczne, oksydowanie czy pasywację stali. W naszym oddziale warszawskim dysponujemy również procesem kadmowania, indowania, srebrzenia, miedziowania oraz ołowiowania. Ponadto istnieje możliwość wykonania chromowania technicznego i niklowania chemicznego wysokofosforowego. Chromowanie techniczne zwiększa twardość powierzchni elementów poddawanych obróbce, a także umożliwia regenerację zużytych czy uszkodzonych detali. Niklowanie chemiczne z kolei jest alternatywą dla chromu i niklu elektrochemicznego. Jest powłoką, która równomiernie rozkłada się na całej powierzchni w przeciwieństwie do wcześniej wymienionych. Dodatkowo po wygrzaniu osiąga twardość zbliżoną do twardości chromu. Nakładanie cieńszych warstw niklu chemicznego powoduje, że można łatwiej sterować procesem, unikając późniejszej obróbki szlifowania do określonego wymiaru. Posiadane przez WZL Nr 2 urządzenie umożliwia także selektywne nakładanie wybranych powłok galwanicznych, co znacznie rozszerza możliwości przygotowywania produktów i realizacji usług zgodnych z indywidualnymi potrzebami klienta.
Inwestycje w Wydział Powłok Galwanicznych nie ograniczyły się do poszerzenia wachlarza zdolności produkcyjnych, realizowanych procesów. Oprócz tego sfinansowano budowę nowoczesnej oczyszczalni ścieków, dzięki czemu prace mogą być przeprowadzane w zamkniętym obiegu wody. Nie tylko chroni to środowisko, ale także poprawia jakość tworzonych produktów i generuje oszczędności.

Autor. Wojskowe Zakłady Lotnicze Nr 2 S.A.

Autor. Wojskowe Zakłady Lotnicze Nr 2 S.A.

Autor. Wojskowe Zakłady Lotnicze Nr 2 S.A.
Badania nieniszczące, czyli szukanie dziury w całym
Badania nieniszczące NDT to kolejna kluczowa usługa bydgoskich zakładów lotniczych, zapewniająca kontrolę jakości produkcji i konserwacji części samolotów. Elementy lotnicze wymagają wysokiej precyzji i pewności wykonania, a Wojskowe Zakłady Lotnicze Nr 2 S.A. posiadają szerokie zdolności do prowadzenia badań metodami nieniszczącymi.
Na czym polegają? NDT to dział badań nieniszczących zmierzających do wykrycia nieciągłości materiału. Wykrywane są wady materiału takie jak: wtrącenia, ubytki korozyjne, pustki, pęknięcia, odwarstwienia, łuski, szczeliny, braki przetopu itp. To tyle suchej definicji, a jak to wygląda w praktyce? W praktyce oznacza to badanie części i zespołów - w przypadku WZL Nr 2 zespołów lotniczych, za pomocą różnych metod oraz różnych środków i przyrządów.
Badania Nieniszczące (NDT) w WZL 2 S.A wykonuje się pięcioma metodami.
Pierwszą z nich są badania penetracyjne (PT, Penetrant Testing), w których stosuje się ciekły penetrant, umożliwiają wykrywanie nieciągłości powierzchniowych. Prowadzi się je na trzech kolejnych etapach – odtłuszczania powierzchni, elektrostatycznego lub zanurzeniowego nakładania penetrantów i nakładania wywoławcza. Badane elementy z nałożonym środkiem są oceniane przez operatorów NDT. Linia do badań penetracyjnych spełnia wymagania normy ASTM-1417.
Druga stosowaną metodą badań NDT jest defektoskopia magnetyczno-proszkowa (MT – Magnetic Testing), która przy użyciu nowoczesnego defektoskopu magnetycznego MAG 50 FR zakupionego specjalnie dla silników F100-PW-229. zwiększenia możliwości prowadzenia badań nieniszczących.
Trzecia metoda to badanie za pomocą prądów wirowych (ET – Eddy Current Testing) w wysokich i niskich częstotliwościach, przy użyciu płaskich i obrotowych sond. Metoda ta umożliwia badanie elementów lotniczych bez potrzeby zdejmowania z nich powłok lakierniczych.
Pozostałe dwie metody to ultradźwiękowa (UT – Ultrasonic Testing) do badań ultradźwiękowych metodą kontaktową oraz rentgenowska (Radiology Testing), która wykonywana jest metodą filmową.
Końcowym etapem takich badań jest określenie stanu technicznego badanych detali oraz w przypadku spełnienia wszelkich norm i warunków, wydanie orzeczenia dopuszczającego badany element do dalszej eksploatacji.
Z uwagi na wagę prowadzenia badań jakościowych w przemyśle lotniczym, wszystkie badania są wykonywane przez najbardziej doświadczony, wyselekcjonowany personel WZL Nr 2 S.A. Każdy pracownik, zanim uzyska tytuł operatora NDT w danej specjalizacji, musi legitymować się doświadczeniem od 400 do 1200 godzin w zależności od specjalizacji, w której zamierza zdobywać uprawnienia. Następnie przyszły adept musi przejść specjalistyczny kurs, po którym otrzymuje uprawnienia, które należy odnawiać co pięć lat.
Personel Działu Badań Nieniszczących jest szkolony i certyfikowany zgodnie z normą EN 4179/NAS 410. Operatorzy NDT prowadzący badania posiadają stopień II w metodach badań: PT, MT, ET, UT lub RT. Najbardziej doświadczeni pracownicy, którzy są gotowi wziąć odpowiedzialność za prowadzenie badań na terenie WZL 2 S.A., po ukończeniu szkolenia i zadaniu egzaminów osiągają stopień trzeci w danej metodzie.

Autor. Wojskowe Zakłady Lotnicze Nr 2 S.A.
Plazma! A co to takiego?
Natryskiwanie plazmowe to kolejna zaawansowana usługa przemysłowa oferowana przez WZL Nr 2 S.A. oddział w Warszawie, polegająca na tworzeniu powłok ochronnych na komponentach silnika lotniczego lub jego naprawie poprzez odtworzenie jego wyeksploatowanych powierzchni. Proces ten polega na nałożeniu materiału proszkowego, zazwyczaj metalicznego lub ceramicznego, na powierzchnię detali silnika za pomocą palnika plazmowego. Proszek jest topiony i natryskiwany na odnawianą powierzchnię, tworząc warstwę o odpowiednich właściwościach. Powłoka plazmowa oferuje rozwiązania dla szerokiej gamy zastosowań w środowiskach o niskiej i wysokiej temperaturze. Proces ten jest niezbędny do naprawy i konserwacji powierzchni detali lotniczych, zapewniając, że pozostaną one zgodne z warunkami technicznymi i będą mogły wykonywać swoje krytyczne zadania.
W 2010 roku w Warszawie na terenie ówczesnego WZL Nr 4 S.A. powstał Wydział Natryskiwania Plazmowego (P-3A, dzisiejsze PCW), który działa do dziś pod nazwą Wydział Usług Mechanicznych i Natryskiwania Plazmowego. Geneza Wydziału Natryskiwania Plazmowego sięga roku 1994, kiedy to dostarczono do zakładu w Warszawie nowoczesne i pionierskie urządzenie do nakładania powłok metodą plazmową, czyli tzw. „plazmotron”. Do dziś urządzenie to realizuje plan produkcyjny remontu części do silników AŁ-21 i RD-33 oraz innych detali lotniczych i komercyjnych.
Równolegle od 2011 roku prowadzone są prace produkcyjne na zupełnie „nowej plazmie”, wyposażając Wydział Natryskiwania Plazmowego PCW nie tylko w innowacyjne urządzenie do nakładania powłok metodą plazmową, ale m.in. także w samodzielną instalację sprężonego powietrza o wysokiej klasie czystości, które jest niezbędne do prowadzenia tego procesu. Należy dodać, że proces nakładania powłok metodą plazmową systemem APS (Atmospheric/Air Plasma Spraying) odbywa się w kabinie w atmosferze powietrza zasysanego z zewnątrz poprzez czerpnie.
Proces ten podobny jest zatem do dość powszechnego dzisiaj procesu napawania. Operacja nałożenia powłoki metodą plazmową nie jest oczywiście taka prosta i ekonomiczna, jakby mogło się wydawać. Generuje niestety duże koszty związane z ogromnym zużyciem prądu elektrycznego, gazów technicznych, drogich materiałów proszkowych, ale także z przygotowaniem detali do natrysku. Części te muszą być odpowiednio osłonięte w związku z wysoką temperaturą cząstek stopionego proszku atakujących ich powierzchnię, które wylatują z płomienia palnika, jak również z możliwością zanieczyszczenia całego elementu natryskiwanego.
Wydział Usług Mechanicznych i Natryskiwania Plazmowego w Warszawie może pochwalić się certyfikacją AS 9100 D oraz najwyżej uznawaną w branży produkcji lotniczej akredytacją Nadcap dla powłok (Coatings). Oprócz remontu detali do silników wojskowych dla Polskich Sił Powietrznych wytwarza również powłoki dla lotnictwa komercyjnego.
Wydział PCW posiada szerokie możliwości rozbudowy i rozwoju, dysponuje młodą i gotową do działania kadrą specjalistów oraz zaawansowanym technicznie sprzętem do nakładania powłok metodą plazmową, a także gazopłomieniową. Urządzeń tego typu mających zastosowanie stricte w przemyśle lotniczym jest w Polsce zaledwie kilka. Wydział Natryskiwania Plazmowego posiada również Laboratorium Weryfikacyjne kontrolujące jakość powłok powstających w procesie. Laboratorium Weryfikacyjne na Wydziale PCW posiada certyfikację Avio Aero oraz General Electric, a także doświadczony personel szkolony przez CCL Metcut (Central Coatings Laboratory) w USA. Jednostka ma zdolność do weryfikacji twardości detali oraz powłok, wykonywania zgładów metalograficznych i ich oceny mikroskopowej oraz analizy wytrzymałościowej warstwy natryskiwanej na naprężenia zrywające.

Autor. Wojskowe Zakłady Lotnicze Nr 2 S.A.
Proces specjalny kulowania automatycznego, czyli shot peening
Kulowanie (shot peening) przekształca naprężenie szczątkowe rozciągające w naprężenie szczątkowe ściskające, prowadzące do znacznego wydłużenia okresu użytkowania części oraz zwiększenia ich obciążalności. Kulowanie to specjalnie zaprojektowany proces zwiększania wytrzymałości zmęczeniowej elementów, które poddawane są silnym naprężeniom. Procedury obróbki powierzchniowej takie jak szlifowanie, frezowanie, gięcie lub obróbka cieplna powodują naprężenie szczątkowe rozciągające. Ten rodzaj naprężenia prowadzi do krótkotrwałego okresu użytkowania części. Kulowanie jest procesem działania na zimno prowadzącym do uzyskania warstwy naprężonej pod wpływem nacisku i modyfikowania właściwości mechanicznych metali śrutem z wystarczającą siłą, aby utworzyć deformację. Kulowanie powierzchni rozprzestrzenia się plastycznie, powodując zmiany właściwości mechanicznych powierzchni. Główną zaletą kulowania jest opóźnienie lub zapobieganie pęknięciom pod naprężeniem rozciągającym.
Proces ten przebiega przez wprowadzenie resztkowego naprężenia ściskającego na powierzchnię elementu. Naprężenie ściskające zapobiega inicjacji pęknięcia, jako że pęknięcia nie mogą rozprzestrzeniać się w środowisku ściskanym generowanym przez kulowanie. Wprowadzenie naprężeń ściskających tą metodą ma jeszcze inne zalety, takie jak np. odprężenie detalu po obróbce skrawaniem, zwiększenie odporności powierzchni na korozję naprężeniową, utwardzenie samej powierzchni detalu i zwiększenie odporności na ścieranie.
Metale o większej wytrzymałości/twardości są bardziej kruche i wrażliwe na powstawanie karbów powierzchniowych. Skłonności te mogą być złagodzone poprzez zastosowanie technologii kulowania, pozwalającej na użycie metali o wysokiej wytrzymałości tam, gdzie łatwo o powstawanie uszkodzeń. Podwozia samolotów dzięki kulowaniu mogą przenosić naprężenia odpowiadające wartości 2068 MPa.
Maszyna do kulowania marki RÖSLER, typ SP 1200 R G1 pracuje w trybie automatycznym, programowana i sterowana, z poziomu komputera. Wyposażona jest w komorę do kulowania ze stołem obrotowym średnicy 1200 mm oraz robota firmy ABB, typ IRB 4600. Emisja medium roboczego, którym jest śrut stalowy CW-28 G3, dokonywana jest przez dwie dysze 10 mm, pionową lancę wewnętrzną lub dyszę obrotową z ręczną wymianą. Proces przebiega zgodnie ze specyfikacją normy SAE Aerospace AMS2432 oraz Agusta-Westland STA100-84-09 rev. D. Obsługę stanowi wykwalifikowany personel o poziomie wyszkolenia potwierdzonym certyfikatami zatwierdzonym przez Federal Aviation Administration (FAA) - Level 2 dla operatorów i najwyższy, Level 3, dla programistów-technologów.

Autor. Wojskowe Zakłady Lotnicze Nr 2 S.A.
Parametrami obróbki są: intensywność, określana na wzorcach - płytkach Almena i pokrycie, badane na umacnianych detalach. Miarą intensywności jest wygięcie płytki, a miarą pokrycia procent usunięcia z powierzchni umacnianej ultrafioletowego śladu flamastra. Dodatkowo nie można spowodować ubytku materiału powyżej ustalonej w normie wartości, przy zachowaniu określonej chropowatości powierzchni. Wielość parametrów powoduje, że powtarzalność procesu musi być zapewniona, jak wspomniano, przez oprogramowanie komputerowe sterujące robotem, stołem obrotowym i automatyką pneumatyczną. Proces przebiega według wcześniej zaprogramowanej, indywidualnie dla każdego detalu, procedury. Materiałami obrabianymi w procesie kulowania są stal węglowa, stal nierdzewna, tytan i stopy aluminium.

Autor. Wojskowe Zakłady Lotnicze Nr 2 S.A.
Znakowanie laserowe
Znakowanie detali pomaga jednoznacznej identyfikacji odnośnie do detalu, jego producenta i niejednokrotnie daty produkcji, dla detali o określonym resursie. W związku z tym WZL2 zainwestowało w nowoczesną znakowarkę laserową DPSS zbudowaną przez firmę Warius, opartą o komponenty renomowanego producenta osprzętu do znakowania laserowego Gravotech. Metoda ta pod kątem efektywności zarówno czasowej, jak i ekonomicznej zostawia daleko za sobą metody klasyczne jak grawerowanie metodą frezowania, nietrwałe znakowanie tuszem, czy nie zawsze estetyczne wybijanie. Technologia DPSS (diode-pumped solid-state laser) pozwala na znakowanie zarówno na powierzchni metali, jak i tworzyw sztucznych.
Zaletą lasera nad wybijaniem czy frezowaniem znaku jest fakt, że laser nie ingeruje w sam materiał, a wypala warstwę rzędu mikronów w górnej warstwie metalu lub powłoki galwanicznej, nie przepalając jej na wylot w drugim przypadku. Wpływ ciepła wiązki jest dla detalu pomijalny. Dzięki temu metoda ta nie ma wpływu na wytrzymałość materiału, nie generuje karbów i niepotrzebnych naprężeń, a także nie usuwa powłoki galwanicznej.
Kolejną zaletą lasera jest czas. W porównaniu z metodą grawerowania CNC przy pomocy frezów (którą WZL 2 także posiada) czas pracy lasera to sekundy w opozycji do metody frezerskiej zajmującej długie minuty. Za efektywnością czasową idzie efektywność ekonomiczna, bo mówiąc kolokwialnie czas to pieniądz, zwłaszcza w odniesieniu do roboczogodziny.
Trzecią nie mniej istotną zaletą jest fakt, że laser pozwala na więcej. Za pomocą znakowarki laserowej można nie tylko wykonać linie, napisy, czy proste znaki, ale także „wypalić” znaki QR – coraz bardziej powszechne w dobie posiadanych przez wszystkich choćby w telefonach skanerów QR kodów. Laserem można też wykonać „odbitkę” fotografii, wykonać bardziej skomplikowaną grafikę, którą będzie można w odcieniach szarości przenieść na detal, choć kolor samego obrazu na detalu zależny jest od samego materiału, na którym grafika jest nanoszona. Dzięki dużej rozdzielczości i szerokim możliwościom, jeśli chodzi o parametry, można uzyskać pożądany efekt.
Znakowarka posiada też przystawkę umożliwiającą znakowanie powierzchni walcowych. Poradzi sobie zarówno ze sworzniem podwozia samolotu, jak i metalowym kubkiem z pamiątkowym grawerem.

Autor. Wojskowe Zakłady Lotnicze Nr 2 S.A.
Artykuł sponsorowany. Partnerem materiału są Wojskowe Zakłady Lotnicze Nr 2 S.A.
WIDEO: Burza w Nowej Dębie. Polskie K9 na poligonie