Czarny koń polskiego programu amunicyjnego. Produkcja przyspiesza
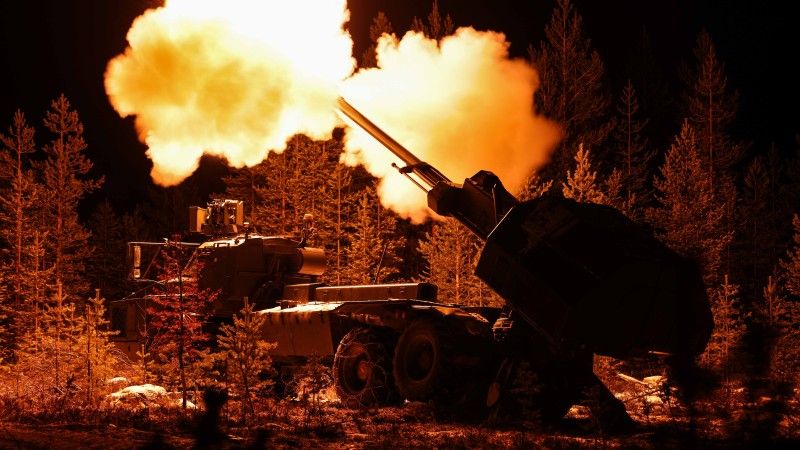
Autor. Corporal Rebecca Brown, RLC / UK MOD
Koncern BAE Systems wkrótce będzie wytwarzał 16 razy więcej amunicji artyleryjskiej niż w 2022 roku. Wszystko dzięki prowadzonym od lat inwestycjom w technologię produkcji pocisków oraz ładunków miotających.
We wrześniu 2023 r. na londyńskich targach DSEI przedsiębiorstwo BAE Systems, jeden z największych producentów uzbrojenia w Europie, zaprezentowało dziennikarzom postępy w programie Next Generation Artillery Ammunition (NGAA). Celem projektu jest stworzenie rodziny środków bojowych kalibru 155 mm o zdecydowanie niższej cenie i szybszych terminach dostaw niż dotąd, a także zastąpienie rodziny amunicji L15 dotąd stosowanej w British Army. Istotne jest też skrócenie i wzmocnienie łańcuchów dostaw w Wielkiej Brytanii, by umożliwić BAE rezygnację z importu surowców (np. materiałów wybuchowych z Francji i USA) oraz podzespołów do wytwarzania nabojów. Wśród środków do realizacji tych zamierzeń wymieniono:
- opracowanie uniwersalnego korpusu pocisku do amunicji wielu typów: odłamkowo-burzącej, oświetlającej, dymnej, cargo itd.;
- zastąpienie stopu stali, z którego dotąd wykonywano korpusy pocisków, odpowiednikiem dostępnym na rynku komercyjnym, lecz o tożsamych parametrach;
- odejście od elaboracji pocisku zalewaniem topliwą mieszanką wybuchową na rzecz technologii mieszania rezonansowo-akustycznego (ang. resonant acoustic mixing, RAM);
- przejście z materiałów wybuchowych na bazie trotylu (TNT) na rzecz plastycznych materiałów kruszących z polimerowym lepiszczem (ang. polymer-bonded explosives, PBX) na bazie heksogenu (RDX);
- stworzenie nowych, przyjaźniejszych środowisku pobudzaczy i spłonek, a także kompozytowego prochu artyleryjskiego na bazie RDX z wykorzystaniem nowej technologii produkcji;
- skonstruowanie nowych zapalników dwóch typów: elektronicznego, programowalnego (e-Fuze) oraz wyposażonego w moduł korekcji toru lotu (ang. course correction fuze, CCF);
- inwestycje w nowe oraz istniejące fabryki w Wielkiej Brytanii, rozproszenie produkcji na większą liczbę zakładów oraz uodpornienie bazy przemysłowej na uderzenia przeciwnika.
Więcej nabojów za niższą kwotę
W BAE Systems postawiono za cel redukcję ceny naboju o między 50 a 75%. Dla porównania, średnia cena samego pocisku odłamkowo-burzącego (bez ładunku miotającego) w Europie jest dziś szacowana na około 4 tys. dolarów, zaś czas oczekiwania na kompletny nabój wynosi około 2 lat. Ponadto, tempo produkcji jest uzależnione od dostaw kluczowych surowców: stopów stali, nitrocelulozy, nitrogliceryny i materiałów wybuchowych, które nie są produkowane w ilościach wystarczających do zaspokojenia zapotrzebowania. Dość przytoczyć polską niezdolność do w produkcji prochu artyleryjskiego (dwu- lub trójbazowego) przez brak odpowiednich kompetencji w kraju oraz zależność od materiałów sprowadzanych z zagranicy.
Według BAE dzięki technologii mieszania rezonansowo-akustycznego czas elaboracji pocisku odłamkowo-burzącego jest liczony w minutach, a nie godzinach. Nowe zapalniki wykorzystują elektronikę dostępną na rynku komercyjnym. To wraz z uniwersalnym korpusem pocisku wykonanego z „cywilnej” stali ma umożliwić włączenie do łańcuchów dostaw podmiotów, które dotąd nie miały nic wspólnego z wytwarzaniem amunicji, a także rozproszenie produkcji w wielu zakładach w zależności od zapotrzebowania. Ponadto, korpus NGAA zaprojektowano w taki sposób, by zagwarantować jego kompatybilność z jak największą liczbą haubic (w praktyce w NATO nie obowiązuje standaryzacja amunicji 155 mm) oraz zmechanizowanych układów zasilania działa w amunicję (tzw. automatów ładowania).
Wdrożenie do produkcji NGAA pozwoli na rozwiązanie kilku problemów jednocześnie. Jeden korpus pocisku będzie wykorzystywany przez kilka typów środków bojowych. To ułatwi integrację z nowymi typami uzbrojenia (upraszczając tworzenie tabel strzelniczych), zwiększy tempo produkcji, a także obniży cenę dzięki zwiększonej skali wytwarzania jednej odkuwki. Dno pocisku jest modułowe. Można tam zastosować tradycyjne ścięcie denne, gazogenerator denny lub silnik rakietowy. Przykładowo, ta sama skorupa znajdzie zastosowanie w pocisku oświetlającym ze ścięciem dennym o donośności nieco ponad 30 km (przy strzelaniu z lufy L/52 w haubicy takiej jak Krab) oraz w amunicji precyzyjnego rażenia, która dzięki silnikowi rakietowemu doleci na 65 km, po czym z pomocą elektronicznego zapalnika z modułem korekcji toru lotu osiągnie kołowy błąd trafienia na poziomie kilku metrów.
Korpus pocisku zaprojektowano z myślą o wyższym ciśnieniu roboczym w komorze nabojowej niż wartości uzyskiwane dziś (do ok. 400 MPa), więc NGAA posiada potencjał rozwojowy. Ponadto, wśród możliwych zastosowań wymienia się wariant cargo przenoszący rozpoznawczy bezzałogowiec. Można domniemywać, że na bazie NGAA może też powstać następca samocelującej amunicji przeciwpancernej BONUS Mk2 (wytwarzanej przez BAE Systems Inc. w Stanach Zjednoczonych na licencji francusko-szwedzkiej). Przedstawiciele koncernu podkreślają też, że nowa amunicja będzie wolna od amerykańskich ograniczeń eksportowych (ang. International Traffic in Arms Regulations, ITAR). W przyszłości firma zamierza przełożyć nową technologię produkcji na amunicję kal. 127 mm stosowaną w armatach okrętowych.
Heksogen prosto z kontenera
Jak informuje „The Sunday Times”, pierwsze efekty przeskoku generacyjnego zaczynają być widoczne w Wielkiej Brytanii. W BAE opracowano technologię produkcji heksogenu (RDX) na dużą skalę w wysoce zautomatyzowanych, mobilnych fabrykach ulokowanych w… kontenerach transportowych, takich jak te stosowane do przewożenia towarów drogą morską i lądową. Dziś materiały kruszące są produkowane w dużych, wrażliwych na ostrzał zakładach, które stanowią oczywisty cel na początku każdego konfliktu zbrojnego. Koncern zamierza produkować 100 ton heksogenu rocznie w każdym takim kontenerze. Jak twierdzą twórcy tego rozwiązania, ma to być tańsze i prostsze niż w przypadku wielkich fabryk. Po uruchomieniu w lecie br. nowego zakładu elaboracji na terenie fabryki BAE w Glascoed w Południowej Walii, poziom produkcji amunicji 155 mm ma wynieść 16-krotność liczb notowanych przed lutym 2022 r. (ówczesnej wielkości produkcji nie podano).

Autor. Cpl Timothy Jones/MOD/OGL v1.0
W niedawnym komunikacie służby prasowe BAE Systems oznajmiły o „dużym przełomie” w produkcji środków bojowych w Wielkiej Brytanii. Od 2022 r. koncern zainwestował ok. 150 mln funtów w istniejące zakłady produkcyjne, a także 8,5 mln w „nowatorskie technologie produkcji” przez ostatnie 5 lat. Dzięki tym nakładom możliwe będzie wytwarzanie materiałów wybuchowych i miotających bez wykorzystania nitrocelulozy oraz nitrogliceryny, które stanowią wąskie gardła w produkcji amunicji (także w Polsce). Firma spodziewa się, że do końca 2026 r. będzie wytwarzała wystarczająco wiele kruszących materiałów wybuchowych i prochu, by w zgodzie z polityką sprzedaży uzbrojenia brytyjskiego Ministerstwa Obrony (ang. Ministry of Defence) móc eksportować je to krajów trzecich.
„Pilotażowy projekt zademonstrował technologiczny przełom w wytwarzaniu materiałów wybuchowych w niewielkim węźle. Ta technologia eliminuje zapotrzebowanie na duże zakłady produkcyjne. Nowo opracowany proch oraz jego technologia produkcji zostały zademonstrowane w szerokim asortymencie produktów, od amunicji karabinowej po wielkokalibrową” – czytamy w komunikacie prasowym. „Nowe technologie powstały z zamiarem redukcji wkładu finansowego i zapewnienia niższych kosztów utrzymania, jednocześnie gwarantując wyższe bezpieczeństwo dzięki produkcji w ciągłym przepływie, co sprawia, że w danej chwili w zakładzie znajduje się mniejsza ilość materiału wybuchowego”.
Polski program amunicji 155 mm
Brytyjski koncern jest uczestnikiem postępowania, które ma wyłonić strategicznego partnera Polskiej Grupy Zbrojeniowej do wspólnej produkcji amunicji artyleryjskiej w Polsce. Środki bojowe kal. 155 mm będą przeznaczone do służących w Wojsku Polskim armatohaubic samobieżnych Krab oraz K9 Thunder. Według Marcina Idzika, członka zarządu PGZ, negocjacje w tej sprawie znajdują się na finiszu. Warto dodać, że BAE Systems jest też producentem ultralekkich haubic ciągnionych M777, armatohaubic samobieżnych M109A7 (w USA) i Archer (w Szwecji). Ponadto, firma jest spadkobiercą Vickers Shipbuilding and Engineering (VSEL) z siedzibą w Barrow-in-Furness, czyli licencjodawcy systemu wieżowego produkowanego w Hucie Stalowa Wola do AHS Krab.
X
" ...wytwarzanie materiałów wybuchowych i miotających bez wykorzystania nitrocelulozy oraz nitrogliceryny," - więc co będzie bazą do prod tych prochów ??? Pytam Redakcję
Antoni Walkowski
Z informacji prasowych wynika, że podstawowymi składnikami nowych plastycznych materiałów wybuchowych (PBX) będzie heksogen (RDX) oraz polimerowe lepiszcze. Będzie to więc nowocześniejsza wariacja na temat heksogenu flegmatyzowanego woskiem (patrz A-IX-1, Kompozycja A), ale przypuszczalnie mniej wrażliwa na działanie bodźców zewnętrznych. Nie mam pewności co do składu kompozytowego prochu. Być może nitrocelulozę zastąpiono lepiszczem na bazie octanu celulozy. Takie dwubazowe prochy opracowano już w ubiegłym wieku.
Sabra
Heksogen czyli Hexamethylenetetramina potraktowana kwasem azotowym
staryPolak
kontener z instalacją do produkcji heksogenu? WOW! szkoda że brak informacji czy będzie możliwy zakup takich "fabryczek"? Chociaż ..... skoro polscy inż już wiedzą że to możliwe .....
doc_doc
Wersja "cargo" mi się podoba. Proponowałem i dalej proponuję wystrzeliwać drona rakietą 122mm np. z WR-40.
Prezes Polski
Ciekawy jestem, czy ktoś się wreszcie obudzi w MON i wpadnie na pomysł, że potrzebujemy amunicji precyzyjniej. Superdrogie pociski typu excalibur to nie jest oczywiście rozwiązanie, ale już zapalnik z układem korekcji jak najbardziej. I o ile jestem sceptyczny co do naszych zdolności w wielu dziedzinach produkcji zbrojeniowej, to myślę, że taki moduł nasz przemysł byłby w stanie opracować.
user_1064174
i pyk kolejny kontrakt za granice