Zawieszenie przyszłości z polskiej firmy [ANALIZA]
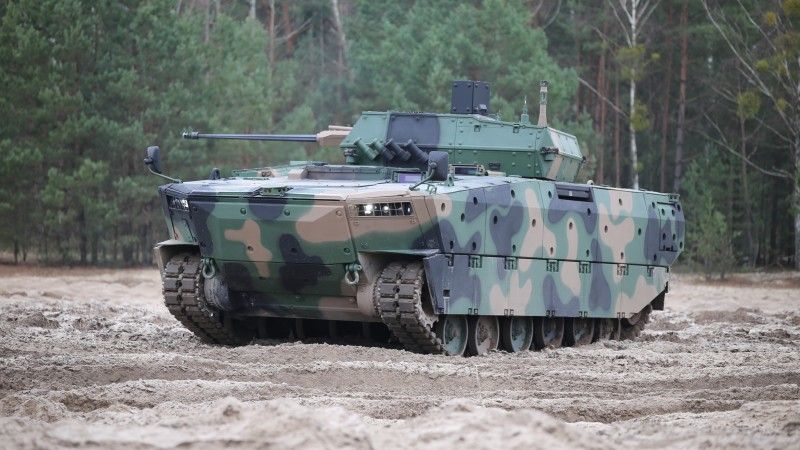
Autor. Marcin Ordon / Defence24
Zawieszenie hydropneumatyczne staje się standardem w broni pancernej. Wiodącym polskim podmiotem w tym dynamicznie rozwijającym się segmencie rynku jest PONAR Wadowice.
Artykuł sponsorowany
Wielkie zakupy ciężkiego sprzętu dla Sił Zbrojnych RP to nie tylko inwestycja w polskie bezpieczeństwo. To też szansa dla krajowego przemysłu obronnego, który otrzymał silny impuls do rozwoju. Jednym z owoców tego procesu są moduły zawieszenia hydropneumatycznego opracowane i produkowane przez przedsiębiorstwo PONAR Wadowice. Dzieło polskich inżynierów to nie tylko odzwierciedlenie światowych trendów w projektowaniu wozów bojowych, ale też rozwiązanie o pokaźnym potencjale rozwojowym.
Najlepszym sposobem na zademonstrowanie zalet zawieszenia hydropneumatycznego jest porównanie go do rozwiązania, które do niedawna stanowiło światowy standard. Przez wiele dekad najczęściej spotykanym układem zawieszenia w wozach opancerzonych były wahacze wleczone resorowane przez drążki skrętne. Trudno o lepszy układ odniesienia, by zilustrować skalę postępu, który dokonał się w dziedzinie układów bieżnych.
Dlaczego nie drążki?
Popularność drążków skrętnych jako elementu resorującego w broni pancernej wynika z kilku czynników. Jest to rozwiązanie proste konstrukcyjnie, o udokumentowanej skuteczności i wysokiej trwałości. Drążki skrętne dysponują wystarczającym zapasem nośności, by znaleźć zastosowanie w pojazdach o bardzo wysokiej masie własnej, choćby współczesnych czołgach podstawowych. Są też zdolne do pochłaniania i oddawania dużej ilości energii generowanej przez układ bieżny ciężkiego wozu o trakcji gąsienicowej.
Jednak rozwiązanie to ma też istotne ograniczenia. Podstawowym problemem jest przestrzeń, którą należy wygospodarować w pojeździe na element resorujący. Najbardziej logiczną lokalizacją dla drążków skrętnych jest dno kadłuba, w poprzek jego osi podłużnej. Po jednej stronie drążek jest mocowany do burty kadłuba, a po drugiej jest połączony z zespołem kołowym (wahaczem wraz z kołem bieżnym). Korpus pojazdu musi być odpowiednio wysoki, by zagwarantować załodze dostęp do samych drążków skrętnych bez konieczności rozebrania wozu na części pierwsze. To przekłada się na wzrost masy kadłuba w stosunku do pojazdu z wózkami zawieszenia mocowanymi na zewnątrz.

Autor. st. chor. sztab. Arkadiusz Dwulatek / CC DO RSZ
Ponadto, obecność drążków skrętnych utrudnia takie zaprojektowanie dna kadłuba, by mogły znaleźć się tam włazy ewakuacyjne dla załogi. W wyniku detonacji ładunku wybuchowego pod kadłubem nierzadko dochodzi do przebicia dna wozu. Uszkodzony lub pęknięty drążek skrętny może stać się pokaźnym odłamkiem, stwarzając poważne zagrożenie dla wszystkich osób przebywających wewnątrz pojazdu.
Drążki zwykle zajmują całą szerokość wozu. Oś drążka jednocześnie stanowi oś obrotu wahacza. Po to, by wahacze po obu stronach pojazdu były zamocowane na tej samej wysokości, koniecznością jest montaż drążków parami, w układzie jeden za drugim. To sprawia, że nie ma fizycznej możliwości, by wahacze (a wraz z nimi koła bieżne) po prawej i po lewej stronie wozu były umieszczone symetrycznie. Przekłada się to na nierównomierne zużycie elementów układu bieżnego po prawej i lewej stronie pojazdu, a także ma negatywny wpływ na właściwości trakcyjne.
W takim układzie nie sposób wyobrazić sobie regulację sztywności zawieszenia – to stała, która wynika wprost z grubości samych drążków oraz właściwości stali sprężynowej, z której są wykonane. Podobnie jest z regulacją prześwitu pojazdu, która bez mechanicznej ingerencji w układ bieżny jest niemożliwa. Pewną alternatywę może stanowić aktywna regulacja siły tłumienia amortyzatora, jednak praktyczne efekty tego rozwiązania są dość ograniczone.
Niebagatelną wadą drążków skrętnych jest złożoność obsługi technicznej, zwłaszcza w wozach o masie kilkudziesięciu ton. Gabaryty, masa i sposób mocowania drążków na dnie kadłuba sprawiają, że wymiana uszkodzonego drążka (na przykład pękniętego w wyniku zużycia lub korozji) pochłania mnóstwo czasu i wysiłku. To ma bezpośrednie przełożenie na gotowość pojazdu oraz jego załogi do realizowania zadań.
Powstały różne modyfikacje drążków skrętnych, które miały na celu zniwelowanie wielu wad tego rozwiązania, chociażby asymetrii pojazdu czy liniowego oporu na ugięcie wahacza. Jednak z racji na szereg czynników żaden z tych pomysłów nie upowszechnił się na tyle, by stać się standardem w branży.
Jeden moduł, wiele podzespołów
Moduł zawieszenia hydropneumatycznego w wozie gąsienicowym jest urządzeniem wielofunkcyjnym. Jego podstawowym zadaniem jest pełnienie roli wahacza, który kontroluje ruch koła bieżnego w płaszczyźnie pionowej. W korpusie wahacza montowany jest element resorujący w postaci sprężyny gazowej. Ta jest wypełniona gazem (najczęściej azotem) fizycznie oddzielonym szczelną membraną od oleju hydraulicznego. Element ten zastępuje tradycyjny drążek skrętny, sprężynę śrubową lub resor piórowy. W module zabudowany jest również amortyzator gazowo-olejowy.
Ruch wahacza sprawia, że rośnie ciśnienie azotu w sprężynie gazowej, która charakteryzuje się nieliniową odpornością na ugięcie. Mówiąc w uproszczeniu, sztywność zawieszenia rośnie wraz ze skokiem wahacza. Wspomniany amortyzator spowalnia ruch obrotowy wahacza, zamieniając energię mechaniczną z jego obrotu w energię hydrauliczną. W ten sposób pełni rolę swoistego tłumika, który łagodzi pracę zespołu kołowego. Charakterystyka pracy tego układu sprawia, że zbędne staje się stosowanie hydraulicznego odboju, który w systemach z drążkami skrętnymi stanowi fizyczny ogranicznik ruchu wahacza.
Zawieszenie hydropneumatyczne tłumi nierówności efektywniej niż układ z drążkami skrętnymi. To przyczynia się do poprawy właściwości trakcyjnych pojazdu w każdych warunkach. Średnia prędkość w terenie jest wyższa, układ bieżny szybciej wraca do neutralnego położenia, stabilizacja uzbrojenia głównego oraz optoelektroniki pracuje mniej intensywnie, a żołnierze na pokładzie (zwłaszcza ci zgromadzeni w przedziale desantu w bojowym wozie piechoty) w mniejszym stopniu odczuwają nierówności terenu. Doskonale widać to po płynności i szybkości, z którą porusza się po poligonie ważąca 48 ton armatohaubica samobieżna Krab.
Zawieszenie hydropneumatyczne ma też inne zalety. Zespoły wahaczy są montowane na zewnątrz pojazdu. To sprawia, że nie ma potrzeby wygospodarowania dodatkowej przestrzeni w kadłubie na drążki skrętne. Ponadto, moduły mają gabaryty niewiele większe od tradycyjnych wahaczy, więc nie występuje potrzeba zwężania kadłuba do określonej szerokości. Jest to niezwykle istotne wobec niezmiennych, „twardych” ograniczeń takich jak maksymalne gabaryty wozu transportowanego koleją lub na zestawie niskopodwoziowym.
Ponadto, w razie awarii lub zużycia możliwe jest zdemontowanie kompletnego zespołu wahacza i instalacja nowego bez konieczności rozbiórki modułu. Uszkodzony element może zostać odesłany do zakładu remontowego na tyłach w celu regeneracji, trafić do wojskowego magazynu, po czym zostać zamontowany na innym, wymagającym naprawy pojeździe. Ten swoisty obieg zamknięty częściami zamiennymi nieco przypomina sposób, w którym nowoczesne siły zbrojne dysponują szybkowymiennymi zespołami napędowymi (ang. powerpack) przeznaczonymi do pojazdów gąsienicowych. To poważne ułatwienie logistyczne dla wojska, a także dogodny sposób na ograniczenie kosztu naprawy kluczowego podzespołu.
Pojazdy gąsienicowe nie obciążają zawieszenia w sposób równomierny. Przykładowo, w nowoczesnym bojowym wozie piechoty największa masa spoczywa na przednich kołach bieżnych, bo to w tej części pojazdu znajduje się ciężki zespół napędowy oraz najgrubszy pancerz. Dzięki regulacji ciśnienia gazu w sprężynie (co umożliwia zmianę prześwitu) oraz charakterystyki tłumienia amortyzatora istnieje możliwość dostosowania modułu zawieszenia do warunków pracy konkretnego koła bieżnego.
Brak drążków skrętnych daje konstruktorowi większą swobodę w nadawaniu kształtu kadłubowi i rozmieszczeniu podzespołów w pojeździe. Nie ma przeszkód, by dno wozu zostało wzmocnione w celu podwyższenia poziomu ochrony przeciwminowej lub ulokowania tam włazów ewakuacyjnych dla załogi. Ponadto, burty kadłuba mogą być w pełni symetryczne, co niweluje problem nierównomiernego zużycia części układu bieżnego po prawej i lewej stronie maszyny.
Unikalne kompetencje
Niewiele firm na świecie dysponuje zdolnością do samodzielnego opracowania modułów zawieszenia hydropneumatycznego do pojazdów gąsienicowych. Niedawno do tego wąskiego grona dołączyło polskie przedsiębiorstwo PONAR Wadowice, które specjalizuje się w hydraulice siłowej. W ciągu ostatnich pięciu lat zrealizowano tam sfinansowany ze środków własnych projekt badawczo-rozwojowy, którego efektem jest opracowanie i wdrożenie dwóch typów pasywnego zawieszenia hydropneumatycznego przeznaczonego do polskich wozów bojowych.
Moduły WHP25 i WHP35 zaprojektowano do pojazdów o średniej masie 25 i 35 ton i o sześciu parach kół bieżnych (tj. na jeden wóz przypada 12 wahaczy). Pierwszy z wymienionych modeli powstał z myślą o wozach bazujących na Lekkim Podwoziu Gąsienicowym opracowanym w Hucie Stalowa Wola. Wśród nich można wymienić między innymi WD (Wóz Dowodzenia) oraz WDSz (Wóz Dowódczo-Sztabowy), które stanowią jeden z fundamentów Dywizjonowego Modułu Ogniowego Regina. Drugi typ zawieszenia jest przeznaczony do Bojowego Wozu Piechoty Borsuk. Drapieżnik ze Stalowej Woli obecnie jest szykowany do produkcji seryjnej.

Autor. Robert Suchy / Defence24.pl
Przyczynkiem do tych prac była polonizacja i rozpoczęcie produkcji kompletnych modułów zawieszenia hydropneumatycznego do armatohaubic samobieżnych Krab rodem z HSW. Doświadczenia wyniesione z tego programu oraz systematyczna rozbudowa potencjału projektowego i produkcyjnego w wadowickim przedsiębiorstwie umożliwiły stworzenie własnego rozwiązania tej klasy, bez konieczności pozyskiwania zagranicznej licencji.
Wadowicki PONAR jest rzadkim przykładem firmy, która może samodzielnie zaprojektować, wykonać prototypy, przebadać i produkować moduły zawieszenia hydropneumatycznego do wojskowych pojazdów gąsienicowych. Porzucenie drążków skrętnych na rzecz nowoczesnych układów bieżnych z wahaczami hydropneumatycznymi otwiera nowe możliwości projektowe polskim konstruktorom ciężkiego sprzętu wojskowego, choćby pod względem dostosowania modułów zawieszenia z myślą o określonym podwoziu.
Moduły zawieszenia WHP25 i WHP35 zostały poddane szczegółowym badaniom przed przekazaniem Hucie Stalowa Wola do montażu na pojazdach. W ten sposób zweryfikowano niezawodność i sprawność wahaczy hydropneumatycznych w niskich (-30° C) i wysokich (55° C) temperaturach, zdolność do działania w słodkiej i słonej wodzie, a także odporność na wysokie ciśnienia (rzędu 900 bar), wibracje i bardzo wysoką wilgotność (93-98%).
Produkt polski
Równie istotnym czynnikiem jest stopniowe uniezależnianie polskiego przemysłu obronnego od zagranicznych licencji oraz importu kluczowych podzespołów. Dzięki pracom prowadzonym w PONAR nad Wisłą budowany jest potencjał produkcyjny i serwisowy w rynkowej niszy, która w większości krajów Europy pozostaje niezagospodarowana. To przekłada się na powstawanie w kraju szeregu wartościowych miejsc pracy, skracanie łańcuchów dostaw, wydatne ułatwienie logistyczne dla wojska, oszczędności dla podatnika oraz budowanie potencjału eksportowego dla unikalnych polskich rozwiązań technicznych.
Cieszy też fakt, że w wadowickim przedsiębiorstwie już trwają prace nad długoterminowym rozwojem ich najnowszego produktu. Moduły WHP25 i WHP35 są pasywne, czyli nie istnieje możliwość zmiany charakterystyki pracy zawieszenia ani regulacji prześwitu przez załogę przebywającą wewnątrz pojazdu. PONAR już dziś prowadzi badania nad autorskimi układami aktywnymi, w których nastawy układu bieżnego są zmieniane całkowicie samoczynnie, także wtedy, gdy pojazd znajduje się w ruchu. Można przypuszczać, że przystankiem na drodze do zawieszenia aktywnego będzie układ półaktywny, w którym regulacja prześwitu oraz tłumienia będzie możliwa w wozie przebywającym na postoju.
Trwająca wojna na Ukrainie przyczyniła się do znacznego wzrostu popytu na hydraulikę z Wadowic. Skala tego konfliktu dobitnie świadczy o konieczności posiadania bezpiecznego łańcucha dostaw i krajowych kompetencji w dziedzinach, które mogą stanowić wąskie gardła w produkcji ciężkiego sprzętu wojskowego.
Polskie zapotrzebowanie na same tylko BWP Borsuk oraz pojazdy specjalistyczne bazujące na jego podwoziu jest szacowane na około 1400 egzemplarzy. Do tego należy dodać spodziewane zamówienia Wojska Polskiego na ciężkie bojowe wozy piechoty, kołowe transportery opancerzone nowej generacji, armatohaubice samobieżne i wiele innych pojazdów.
Polonizacja układów bieżnych w tych pojazdach jest nie tylko szansą na dynamiczny rozwój dla małopolskiego przedsiębiorstwa, ale też koniecznością z punktu widzenia Sił Zbrojnych. Dlatego warto przyglądać się nowościom z firmy PONAR Wadowice, nowego w tym segmencie rynku gracza, który wkrótce może stać się regionalnym potentatem w specjalistycznej branży.
Artykuł sponsorowany
Był czas_3 dekady
Twierdzę, że moglibyśmy opracować czołg i byłby NASZ., taki jaki chcielibyśmy mieć (HSW, Bumar, WZM Poznań, WB+AREX, PCO...).
Takijeden
A taki jeden forumowy kolega z nickiem na D twierdził, że Polacy że współpracy z Koreą nic nie mają, że tak naprawdę jesteśmy dla nich montownia tych elementów i nie ma żadnego transferu technologii.
Chyżwar
On programowo jeździ po zakupach w Korei i Wielkiej Brytanii, bo to konkurencja dla jego ulubionych Niemców. Nie powie słowa przeciwko Izraelowi nawet wówczas, gdy na jaw wychodzą ich zbrodnie wojenne. Do tego, co kupujemy w USA się nie czepia. Przynajmniej na razie. Zobaczymy co będzie wypisywał jak tam wygra Trump. Realia natomiast są takie, że gadanina o "strategicznym partnerstwie" z Koreą, Niemcami, czy USA" to polityczny frazes. Dla tych państw liczymy się jako klient kupujący broń. Można ugrać więcej. Można mniej. W USA udało się ugrać sporo. Na Niemcy nie ma po co patrzeć, bo to manufaktura jest. W przypadku Korei dałoby się ugrać więcej niż w USA. Tylko trzeba chcieć. Faktyczne partnerstwo jest z Brytolami. Bynajmniej nie dlatego, że oni są tacy dobrzy. Jest tak dlatego, bo oni zdają sobie sprawę z tego, że ich przemysł nijak nie wyprodukuje tego, co tam zamówiliśmy.
RGB
Wnioskując z tekstu artykułu zawieszenie Borsuka może mieć nośność 35 ton, czyli ma jeszcze 7 ton zapasu. A tak ogóle, to duża rzecz że mamy w Polsce firmę która opracowuje tak zaawansowane rozwiązania jak zawieszenia hydropneumatyczne. Szczególnie obiecująco wygląda projekt aktywnego zawieszenia hydro.
Chyżwar
Mylisz się. Swego czasu bawiono z Bradleyem i zrobiono demonstrator technologii z dziesięcioma elementami podobnego zawieszenia. Zwiększono ciśnienie Azotu i obciążono wóz tak, że ważył aż 45 ton. Zawieszenie dało sobie radę. Choć sądzę, że podczas normalnej eksploatacji nie wytrzymało by długo. Borsuk ma dwanaście elementów a spec zajmujący się tematem i znający tą konstrukcję twierdzi, że bawiąc się ze zwiększaniem ciśnienia Azotu rozsądny margines to od 8 do 11 ton więcej. Zobaczymy jak Amerykanom pójdzie z Bradleyem. Oni obecnie na wszelki wypadek jakby program nowego BWP im nie wypalił już od jakiegoś czasu testują Braleya z dwunastoma modułami. I nie są to już demonstratory technologii tylko prototypy a kasy na eksperymenty mają więcej niż my. Poza tym DMC to wartość umowna. Kiedy Brytole projektowali Challengery 2 nie przypuszczali, że ten już wtedy ciężki czołg utyje do granicy absurdu. I mimo, że utył jakoś jeździ z tym samym zawieszeniem.
RGB
Chyżwar może i jest tak jak piszesz nie mam tu dostatecznej wiedzy żeby się w tej kwestii wypowiadać. W tekście zatwierdzonym przez producenta jest informacja o 35 tonach, a to już pozwala dopancerzyć Borsuka do pełnej szóstki z przodu i czwórki z boków. Mówi się też ze moduły wypornościowe po bokach ważą po tonie każda, wiec i tu jest na czym oszczędzić.
Chyżwar
@RGB Człowiek, którego mam na myśli popełnił sporo artykułów. Między innymi o polskich pancerzach reaktywnych i ceramicznych. Nie podam ci linka, bo mod pewnie by to wyciął. Ale jeśli zechcesz, łatwo znajdziesz. CV-90, który w założeniu miał pływać, ale nie pływał, bo kiedy go konstruowano technologia stała na zbyt niskim poziome żeby zapewnić mu właściwą osłonę też zaczynał jako stosunkowo lekki wóz. Tymczasem ostatni jego wypust to już 40 ton. Ciężki BWP to jedno. Ale trzeba zdać sobie sprawę z tego, że zanim powstanie i będzie gotowy do produkcji miną lata. Dlatego uważam, że pilniejszą rzeczą jest opracowanie ciężkiego pancerza dla Borsuków. Niechby sobie takie pancerze leżały w magazynach gotowe do zamontowania w razie "W". A w czasach pokoju niech wóz jeździ taki, jaki jest, żeby nie forsować powerpacka i zawieszenia. Z elementami dodatkowego pancerza dla Rosomaków, którego dorobiły się przez Afganistan postępujemy przecież tak samo.
Dudley
To może wykorzystać dobre doświadczenia, i zlecić zaprojektowanie takiego zawieszenia do Leo2Pl , i zastosować je w Leo2a5. Dla 250 maszyn może się opłacić, skoro opłaciło się dla 120 Krabów. Firma przy tym może zostać poddostawcą, koncernów zbrojeniowych na świecie, o ile będzie konkurencyjna.
Chyżwar
Myśl jest przednia, choć niesetny ekstremalnie trudna do zrealizowania. Na tych Leosiach łapska trzymają Niemcy, którzy jak każdy inny producent nie lubią kiedy się coś robi bez autoryzacji z ich strony. A nie lubią do tego stopnia, że nawet z wymianą radiostacji na inne niż ich jest problem. Gdybyś chciał takie zawieszenie do M1 ono też by nie przeszło dokładnie z takich samych powodów. Choć tu jest o tyle dobrze, że Amerykanie sami kombinują z hydropneumatyką, więc pewnie przy okazji modernizacji będzie można skorzystać z ich własnych rozwiązań. Nie będzie to co prawda krajowy produkt, ale ze względu na techniczne zalety takiego rozwiązania warto by było się nad nim pochylić.
Prezes Polski
Po co? Leo jest i jeździ. Zmiana zawieszenia nie zwiększy radykalnie walorów bojowych a będzie kosztować krocie. Mamy w co wkładać kasę.
Chyżwar
@Prezes Polski Otóż zmienia. I to sporo. Po pierwsze po najechaniu na minę drążki skrętne jak przebiją dno przedziału bojowego zachowują się tak samo jak odłamki granatu, podczas gdy w przypadku zawieszenia hydropneumatycznego to zjawisko nie występuje. Po drugie tego typu zawieszenie pozwala na znacznie bardziej elastyczne podejście do dopancerzenia pojazdu. Po trzecie jak pierdyknie taki moduł to w warunkach polowych odkręca się go i przykręca nowy a uszkodzony jedzie sobie do warsztatu gdzie się go naprawia.
"Pułkownik" Michał
Sukces rodzimego przedsiębiorstwa zawsze cieszy! :D
Chyżwar
Podobnie jak pochodzący z krajowej produkcji istotny element w konstrukcji Borsuka. Ale i tak wielu śmiesznych ludzików będzie pluło na ten wóz.
Melaq84
No miało być naplucie a wyszło w plusie że są takie możliwości krajowe. 1 dnia nie zbudowano Rzymu ani borsuka Pozdrawiam;)
X
Widzę że jesteś zawiedziony... :/